The manufacturing industry inculcates a rich history of technological evolution. It has consistently embraced change and disruption over the last hundred years. Adoption of Industry 4.0 principles and smart manufacturing have flourished during the pandemic where new technological innovations have accelerated and been adopted by manufacturers – causing a shift to a new era of smart manufacturing leveraging digital transformation.
The technological advancement of industry 4.0 technology foundations such as AI (artificial intelligence), IIoT (Industrial Internet of things), big data & analytics gave confidence to manufacturers to deploy industry 4.0 led smart manufacturing at scale, moving away from discrete POCs (proof of concepts). Adoption of such new-age technologies enabled manufacturers not only to achieve operational excellence and efficiency but also enabled them to see game-changing business insights that essentially help them to reduce operating costs, to better engage with their customers, partners, and suppliers, and to manage their assets in a much efficient manner. The unprecedented level of integrations across suppliers, manufacturing shop-floor systems, and customers have generated enormous value across the entire production process and supply chain. It is evident that such transformation has allowed a great level of collaboration between humans and machines, giving rise to a new perspective of productivity, efficiency, and managing quality.
There are many definitions of Smart Manufacturing, and they are all correct in their own right. In a simple view, smart manufacturing delivers a fully integrated and collaborative manufacturing setting with real-time visibility and capability to address the changing needs of the market (or customers) in a much more flexible way. Smart manufacturing starts by, at minimum, connecting all the assets (Physical, environmental, and human capital) and monitoring them under a single platform, significantly improving transparency, traceability, and employee health and safety. Thanks to technology and services such as Sensors, RFID, IIOT, Telematics, and Cloud. Cloud technologies and high-speed networks have made it possible to manage shop floor monitoring more accessible and convenient. Real-time visibility of physical assets improved production planning and execution much more efficiently. Further, a Smart Manufacturing operation permits manufacturers to reduce unplanned machine downtime and improve machine maintenance schedule, creating a positive impact on CAPEX (Capital Expenditure) allocation for physical assets and improved delivery of products to end customers.
Below are three crucial goals achieved by businesses adopting the concept of smart manufacturing:
Data-driven Decision Making
Smart manufacturing facilitates a data-driven approach. It allows gathering data across the supply chain leveraging Sensors, RFID, and IIOT and data from a system of records such as ERP, CRM, and other data sources. Smart Manufacturing deployment architecture also suggests creating a centralized data management that can eliminate data duplication, improve data consistency, and allow organizations to find deep business insights. Centralized data platforms and modern AI/ML technologies comes very handy, primarily to address use cases such as spend analytics, procurement analytics, predictive machine maintenance, demand, and production capacity forecasting, track, and trace assets, etc.
Improved Productivity
Smart manufacturing processes provide deeper access to data across the entire supply chain. Real-time data outlines what the manufacturer needs, when and how the raw materials need supply, and how stock needs to move, making the supply chain highly efficient and productive. Deploying smart manufacturing tools help in identifying defects in the production process much better, thereby reducing waste. Technologies such as AI further help to predict possible manufacturing defects and enhance product accuracy, enhancing productivity to a great extent. Smart Manufacturing also focuses on automating redundant processes, enhancing process accuracy, efficiency and helping manufacturers optimize their workforce for more productivity and value-driven tasks.
Innovation and Better Quality
When productivity is improved, it saves money that can be re-invested in product innovation. Transparency in the process provides greater visibility regarding gaps in quality, which essentially becomes the foundational stone towards delivering better quality by mitigating current and predicted quality gaps. Complete visibility of the production process reduces the cost of quality by reducing the number of production rejects.
Wrap Up
The advancement of technological aspects has undoubtedly aided in building an effective & efficient manufacturing system. With industry 4.0, the manufacturing sector has become more resilient. Technologies such as AI, IoT, and big data increase operational efficiency, minimize costs and enhance overall productivity. It also helps improve predictability and enables effective decision-making. With the help of smart factory manufacturing, businesses can respond to dynamic market needs. Hence, they must adapt to this concept to reap the benefits.
About the Author:
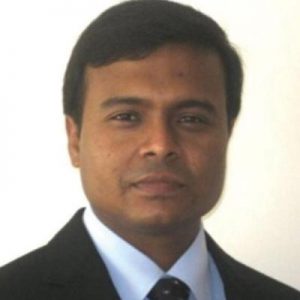
Rajen Ghosh is a transformation leader with 17+ years in IT Industry working across Middle east, Americas and Europe. He comes with the background of different verticals like Health Care and Pharmaceuticals, Manufacturing, Financial Services, FMCG and Utility. He is a vivid speaker and loves to speak on Technology Transformation in Industry forums as well as with the Analyst & Advisor community.